Over 1,000 successful forming projects!
What is the Aluminum Forming Research Center?
The Center was established as a step towards a new type of manufacturing by Takano Co., Ltd. (a precision sheet metal company in Matsumoto City, Nagano Prefecture) in 2019.
The center deals with aluminum forming using metal 3D printers based on Takano’s core strengths of technical capability (3D design and metal processing) and quality control capability. The center works to promote the utilization of metal 3D printers from Nagano Prefecture to all over Japan and the rest of the world.
(Selected as an FY2020 Small and Medium Enterprise Agency Japan Brand Development Assistance Program project and Japan External Trade Organization (JETRO) Consortium for New Export Nation Program)
Our strengths
- Metal processing knowledge cultivated through precision sheet metal business: Realization of high-quality manufacturing based on a foundation of the metal processing technical capabilities we have cultivated through our precision sheet metal business (50 years of history)
- Metal 3D printer forming track record: We have a proven track record in a diverse range of forming focusing mainly on automotive parts and precision device manufacturers (Over 1,000 cumulative projects completed)
- Forming quality based on research and testing: Numerical evaluation of everything from metal laminate forming basic properties to formed product quality through collaboration with research institutes (collaborations with industry, academia, and government)
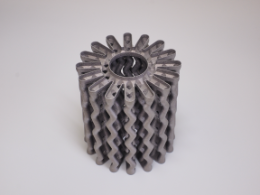
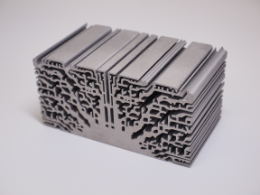
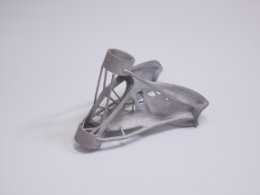
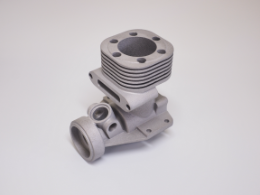
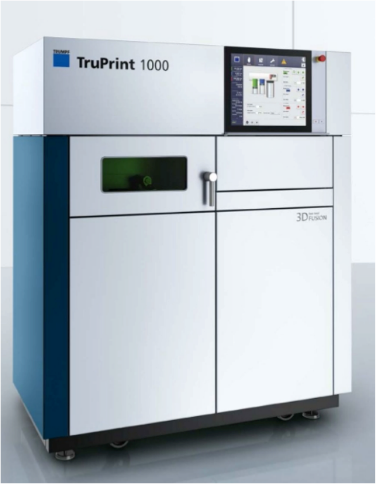
Equipment | TruPrint 1000 (TRUMPF) |
---|---|
Build capacity | Φ96mm × H75mm |
Materials | Aluminum (AISi10Mg), contact us for a consultation. *We can also handle materials other than aluminum (resin, stainless steel, etc.). |
Powder particle size | 40 μm or smaller |
Single layer overlay thickness | 20μm |
Precision | Approximately ±0.1 mm |
Surface quality | Ra 5 to 10 μm |
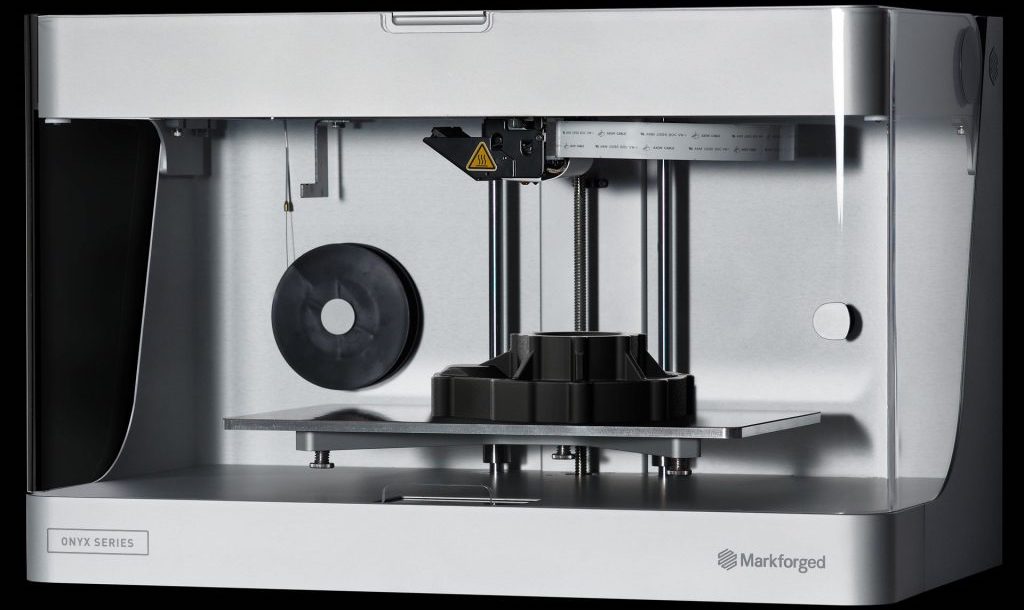
Equipment | Mark Two (Markforged) |
---|---|
Build capacity | 320mm × 132mm × 154mm |
Fiber materials | Carbon fibers, fiberglass, high temperature fiberglass, Kevlar |
Layer height | 100μm |
Precision | Approximately ±0.1 mm |
Aluminum formed product properties
Aluminum powder materials
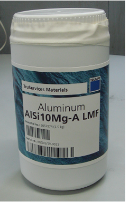
AlSi10Mg is an aluminum casting alloy with good casting properties and is the most common powdered material used to the degree that “aluminum for metal 3D printing” almost always refers to AlSi10Mg. The material has favorable strength, hardness, and dynamic properties, and is well-suited to prototype forming aimed at decreasing weight, integrating components, forming complex shapes, forming hollow cavities, and other advanced processing. The material can also be machine processed, electric erosion arc machined, welded, ground, painted, surface processed, or coated as necessary.
Tensile strength, yield strength, elongation, degree of elasticity, hardness
Test | Tensile strength (MPa) |
Yield strength (MPa) |
Elongation (%) |
Degree of elasticity (GPa) |
Hardness * (HV) |
---|---|---|---|---|---|
0° | 472 | 293 | 10 | 67 | 132 |
90° | 468 | 280 | 6 | 63 | 127 |
All data are the average values from 3 test pieces.
*:Hardness was measured at 8-9 points per test piece, with no deviations found for each location
【[Reference] Aluminum die-cast products: Tensile strength: Approximately 310 MPa, General purpose aluminum alloy: Tensile strength: Approximately 260 MPa
Formed product cross-section and internal defect observation data
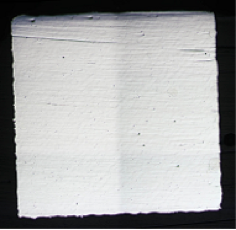
Cross-section observation
by metallograph (90°)
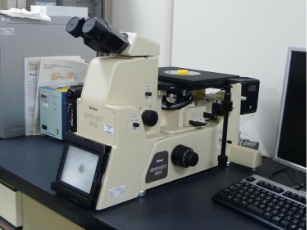
Nikon
EPIPHOT300
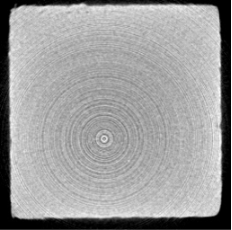
nternal defect observation
by X-ray CT (90°)
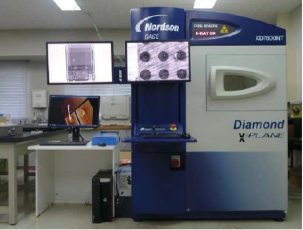
DAGE
XD7600NT Diamond
The above are the test results (from tests implemented at the Nagano Prefecture General Industrial Technology Center) from test pieces, and are not guarantees regarding the performance, capacity, or properties of other formed products.
Examples
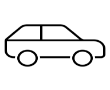
Automobiles
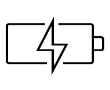
Batteries
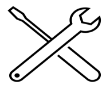
Tools
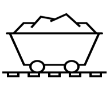
Materials
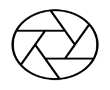
Optics
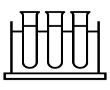
Chemicals
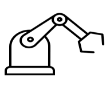
Robots/
equipment

IT/
communications
Example solutions from our company’s formed products are listed below.
Please contact us for further details on any of our solutions.
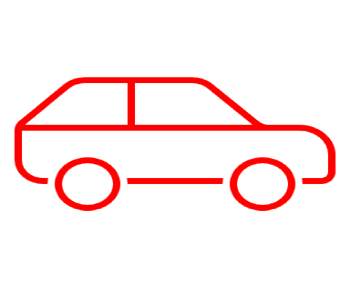
Industry
Automotive industry ①
Customer issues:
The customer wanted to create prototype intake pipes in complex shapes.
TAKANO Solution
Pipes were formed using metal 3D printers and other parts were formed using machine processing. Welding was carried out by our company to create the products which the customer desired. (Turnaround time: 7 days)
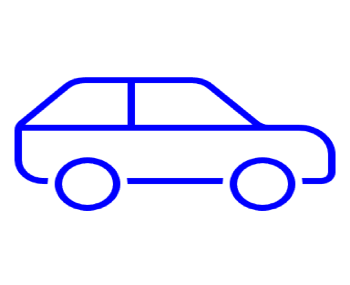
Industry
Automotive industry②
Customer issues:
The customer wanted to create prototype heat sinks with complex shapes and thin plate thickness.
TAKANO Solution
We worked closely with the metal 3D printer manufacturer to prepare machine parameters specialized for this particular customer. We created the “complex shape” and “thin plate thickness” heat sink prototypes which the customer desired. (Turnaround time: 7 days)
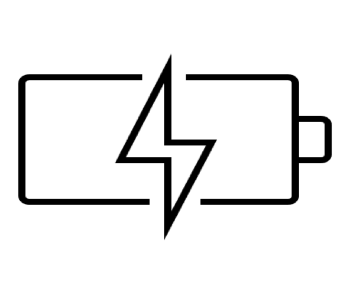
Industry
Automotive industry③
Customer issues:
The customer wanted to create metal with a low apparent density.
TAKANO Solution
Creating a metal with a low apparent density was a difficult issue。However, we were able to produce the formed products as desired by finely tuning machine parameters. This project also resulted in us being able to produce “worn metal” and “metal which water could permeate”. (Turnaround time: 3 days)
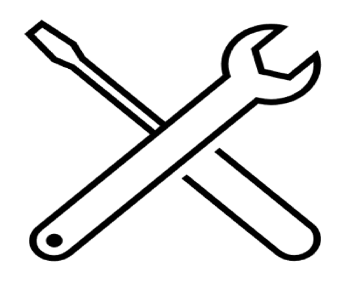
Industry
Tool industry
Customer issues:
The customer wanted to form complex shape prototypes which could not be formed using conventional machining.
TAKANO Solution
We were able to form the complex shapes the customer desired while still maintaining the material strength. In addition, we were also able to make lighter weight and vibration resistant tools in some cases by using an internal honeycomb structure. (Turnaround time: 7 days)
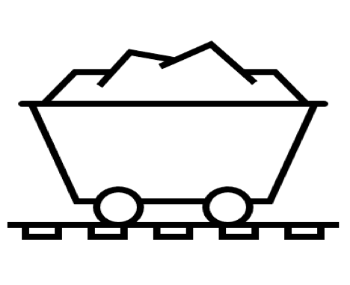
Industry
Materials industry
Customer issues:
The customer wanted to form special parts to be used in in-house production lines. They asked us to do everything from creating 3D data from 2D drawings to carrying out 3D printing.
TAKANO Solution
We received 2D drawings from the customer and then carried out everything from creation of 3D data to 3D printing. We continue to receive orders from this customer for prototypes with slightly altered shapes. (Turnaround time: 5 days)
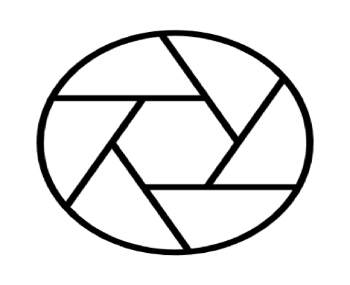
Industry
Optics industry
Customer issues:
The customer wanted to form parts for light collecting components with holes which could not be formed using conventional machining.
TAKANO Solution
We carried out repeated detailed meetings with the customer and were able to form the products according to their requests. Please contact us for a consultation if you any specific desired hole sizes or shapes. (Turnaround time: 2 days)(制作日数2日)。
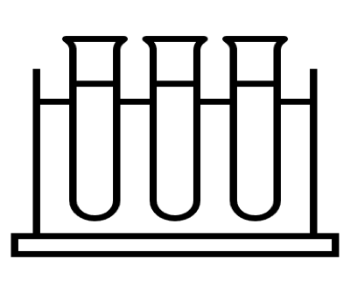
Industry
Chemical industry
Customer issues:
The customer wanted to create research components out of mesh shapes and copper materials.
TAKANO Solution
As our company doesn’t handle copper materials, we instead copper plated the parts after forming. We have a proven track record in a variety of prototype products including mesh structures, lattice structures, honeycomb structures, and more.
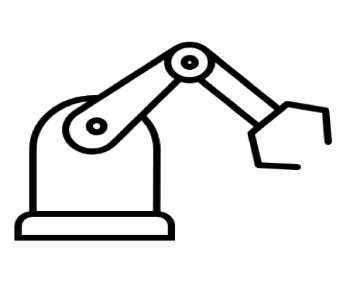
Industry
Robotics industry
Customer issues:
The customer wanted to form prototype parts for construction equipment.
TAKANO Solution
In addition to carrying out frequent data exchanges, we also visited the customer and were able to form the customer’s desired products through repeated, close collaboration. (制作日数2日)。
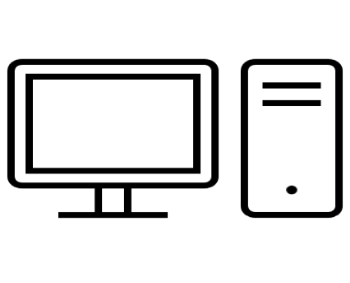
Industry
IT/communications industry
Customer issues:
The customer wanted to form equipment bodies out of aluminum materials. The customer wanted us to not only help them reduce costs, but also use specialized R processing.
TAKANO Solution
After discussing with the customer, we determined that sheet metal was more suited to the customer’s needs than 3D metal printing, so we carried out the project using sheet metal processing. Processing of aluminum sheet metal is another of our company’s strengths. We can provide optimal products to fulfill your needs.
TAKANO samples
These are samples of some of the products our company has manufactured.